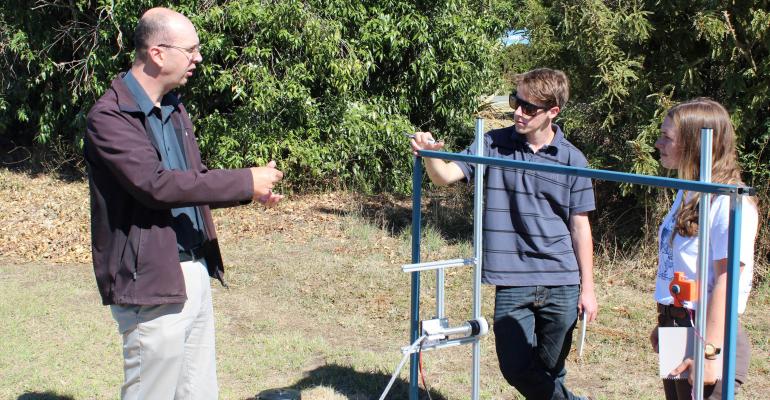
Dr Scott Post
Hitting the mark
Most horticultural spraying uses air-blast sprayers, which fire droplets of fertiliser or insecticide in a cloud around the orchard or vineyard, hoping that each leaf will be covered.
It works, but not efficiently.
Usually only around 30 percent of the product hits and sticks to the trees and plants, leaving the other 70 percent languishing on the ground or drifting away in the air – potentially polluting the environment, and generally wasting product.
But SfTI Seed researcher at Lincoln Agritech Dr Scott Post is working to improve the fraction of the spray that hits the target.
Scott and his team are tackling this problem with two related pieces of science – a novel electrostatic sprayer nozzle, and an ultrasonic sensor that can shut sprayer nozzles off and on.
“If you imagine any orchard, vineyard, or crops like potatoes, there are always gaps where there aren’t any plants, as well as the turn-around areas at the ends of the rows.
“We’re working on a sensor that can tell when there’s no plant material in the rows, or if the spacing between plants isn’t even. The sensor feeds the data to a computer controlling the sprayer and turns it on and off at the right times.”
The sprayer is electrostatic.
“The idea is that you put an electrode on the sprayer nozzle, which charges the droplets as they come through it. They shoot into the air, and because they’re charged, they’re looking to earth themselves as quickly as possible, which attracts them to the plants. They’re also slightly repelled from each other, so they’ll try and spread themselves out. That’s what gives you a thin, uniform coverage layer.
“With the right manipulation of the electric field in the air, droplets will even fly out of the sprayer and then defy gravity by heading upwards to coat the underside of leaves.”
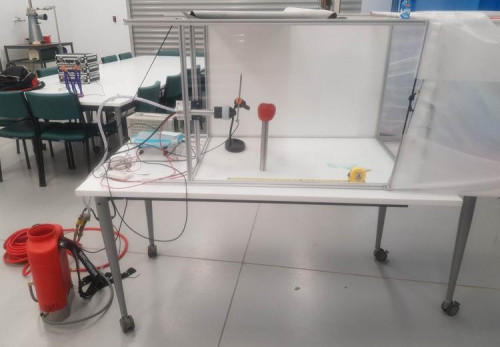
To get the droplets flying in formation, Scott is using computer simulation with the support of team members Mark Jermy and Paul Gaynor and students at the University of Canterbury, who are taking the project from computer simulations and lab testing all the way to field trials.
“We’re working on nailing down what is exactly the right amount of charge, drop size and drop speed,” Scott says.
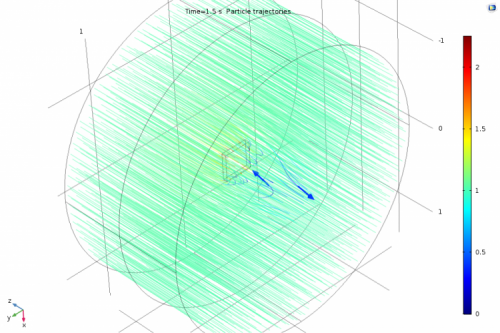
At the same time, they are iterating a new nozzle design using the university’s Rapid Prototype Machine (3D plastic printer).
“Plastic’s a good material, because it doesn’t conduct and interfere with the electrode,” Scott says.
The world market for a more efficient charged nozzle could be huge.
Scott says the team are already confident they can improve efficiency from the typical 30 percent to at least 50 percent, just with the new nozzle alone.
“And I think we’ll be able to do a lot better than that. With improvements in efficiency from using a lot less product spray, and a more cost-effective nozzle design, you’d start to make your money back.
“I think if we can achieve that, in tandem with the droplets going precisely where we want them to, people will start to get very interested.”
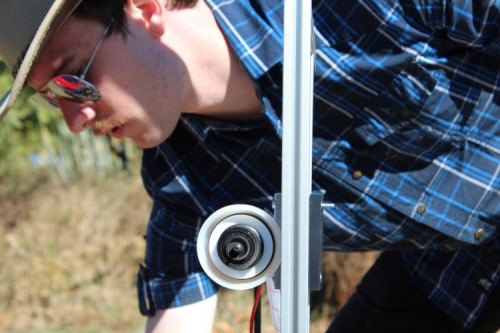
Top image: Dr Scott Post explains the project to University of Canterbury students Rhys Fitzgerald and Rachel Schultz.