Ending with impact: New technological first for forestry
Like a robotic vacuum cleaner that maps out and cares for your living room, SfTI researchers are turning forestry tools into a heavy-duty, self-navigating, smart machine that will independently munch its way along overgrown forestry service tracks.
The autonomous track maintenance tool is an idea that evolved from our $5 million Spearhead research project that has been focusing on robotic technology over the five years to June 2022. That team successfully delivered a quad-bike-sized, self-navigating robot, which they demonstrated to members of the Lake Taupo and Lake Rotoaira Forest Trusts, local iwi and the public in June 2022. The robot inspired strong interest, and with the support and partnership of the industry, the team has been awarded an additional $1 million to deliver a boosted version.
It’s part of a new suite of SfTI funding to enable our most promising Spearhead research projects to ‘end with impact’. All National Science Challenges, including SfTI, will draw to a close in June 2024 and it’s vital that every drop of practical impact from our research is delivered. In a 2022 funding round, our Spearhead projects were invited to put forward ideas that have germinated during their work of the past few years, and that with more time and investment could reap impactful rewards. Working directly with the industry is an important feature of these research projects.
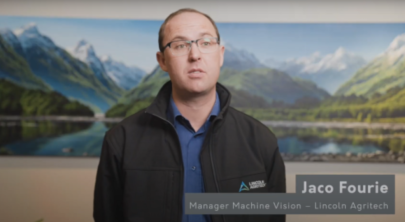
Lincoln Agritech’s manager machine vision Jaco Fourie was part of the original robotics Spearhead research team and will lead the new phase.
“Once we had proved the science worked, we sat down with industry to find out what kinds of applications would be most helpful to them, and track clearing is what the forest owners decided on.
“Once we had proved the science worked, we sat down with industry to find out what kinds of applications would be most helpful to them, and track clearing is what the forest owners decided on.
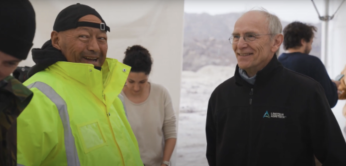
Lincoln Agritech’s manager precision agriculture Armin Werner led the original robotic spearhead project and says the team made a lot of progress in understanding how sensors worked in a younger forest.
Image: Armin at the Feild trial liaising with industry.
To cope in mature forests, the new robotic platform will be a big step up from the quad-bike-sized demonstrator. It will run on rubber tracks, like a small digger and will crawl along forestry tracks drawing in saplings, broom, gorse, blackberry and other slash as it goes, leaving only mulch behind. Machinery like this already exists around the world for clearing land but is not used in forestry. These existing machines are remote-controlled, meaning an operator has to be with the machine at all times, deciding its direction and ensuring the safety of workers and others in the forest.
The SfTI ending with impact project will put together a package of sensors, software, machine vision technology and hardware to enable the mulcher to progress along tracks on its own. Eventually its optical and thermal machine vision will allow the forest robot to ‘see’ workers in the forest, even when obscured by foliage and replot an alternative path autonomously.
“Our path maintenance robot won’t be quite self-docking out of its shed like a robot vacuum cleaner, but you’ll be able to launch it from a roadside trailer, and it will return to that spot when it’s done clearing tracks for the day,” Jaco says.
“We’re focused on the mulching tool initially, as that’s what industry wants, but in the future the same platform could carry other tools, like sprayers and tree thinners. You’d just hook up whatever equipment you needed on the front.
“There’s been a big advantage from working closely with industry. As researchers, we can get very excited in front of a whiteboard talking about possibilities, but our industry partners will always ground our discussions with questions like ‘can I put that on the back of a ute or a trailer?’,” Jaco says.
“There’s been a big advantage from working closely with industry. As researchers, we can get very excited in front of a whiteboard talking about possibilities, but our industry partners will always ground our discussions with questions like ‘can I put that on the back of a ute or a trailer?’,” Jaco says.
Having the robot to do work that is currently done by people will mean they can receive training for additional skills such as supervising and maintaining the robot. This includes allocating its jobs, bringing it to sites and managing it through an internet-based dashboard. They can also step in if the robot gets stuck and remotely help it move around obstacles. It’s hoped this will help make a career in forestry more attractive for the next generation of workers. Skilled staff will also be needed for maintenance, servicing and repair.
The team have started assessing options for the base platform and planning test tracks on Whenua owned by Lake Taupo and Lake Rotoaira Forest Trusts, which they will use to put the prototype through its paces.
Track clearing is vital to silviculture. As well as giving access to planting, thinning, spraying, soil sampling and monitoring forestry health, tracks are also key for quantifying and eradicating pests. Track hygiene requires that they be manually cleared every two to five years, which currently requires two or three people taking two days per track to keep down the overgrowth. With hundreds of kilometres of tracks running through the forests – it’s a heavily time and resource-intensive task. The SfTI machine will be able to clear the tracks every six months using only one person’s time to supervise and taking less than an hour per track.
“It’s exciting to be working on a final application for our research that foresters are going to be able to actually use, and that can benefit them in a wide variety of ways. In the future there will be other options for the products we can offer foresters, as well as other applications,” Jaco says.
The project is funded for $1,000,000 to March 2024. Read about all of our ending with impact projects.